Piping Design
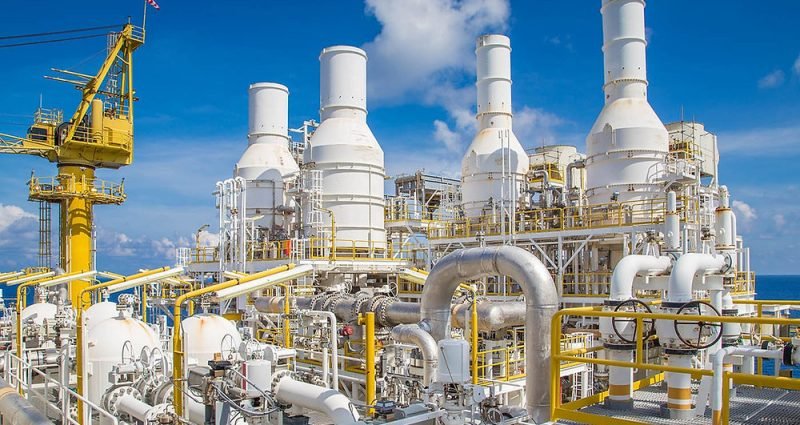
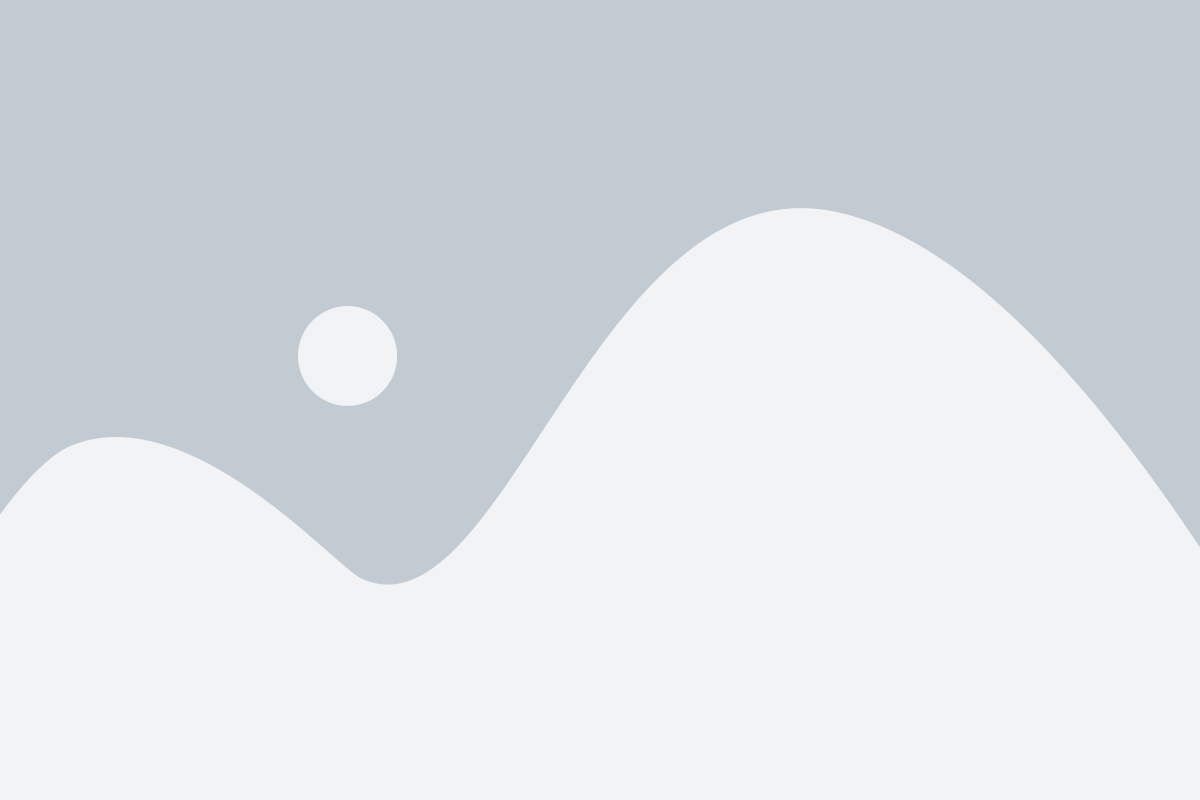
5 Months - 120 Hrs
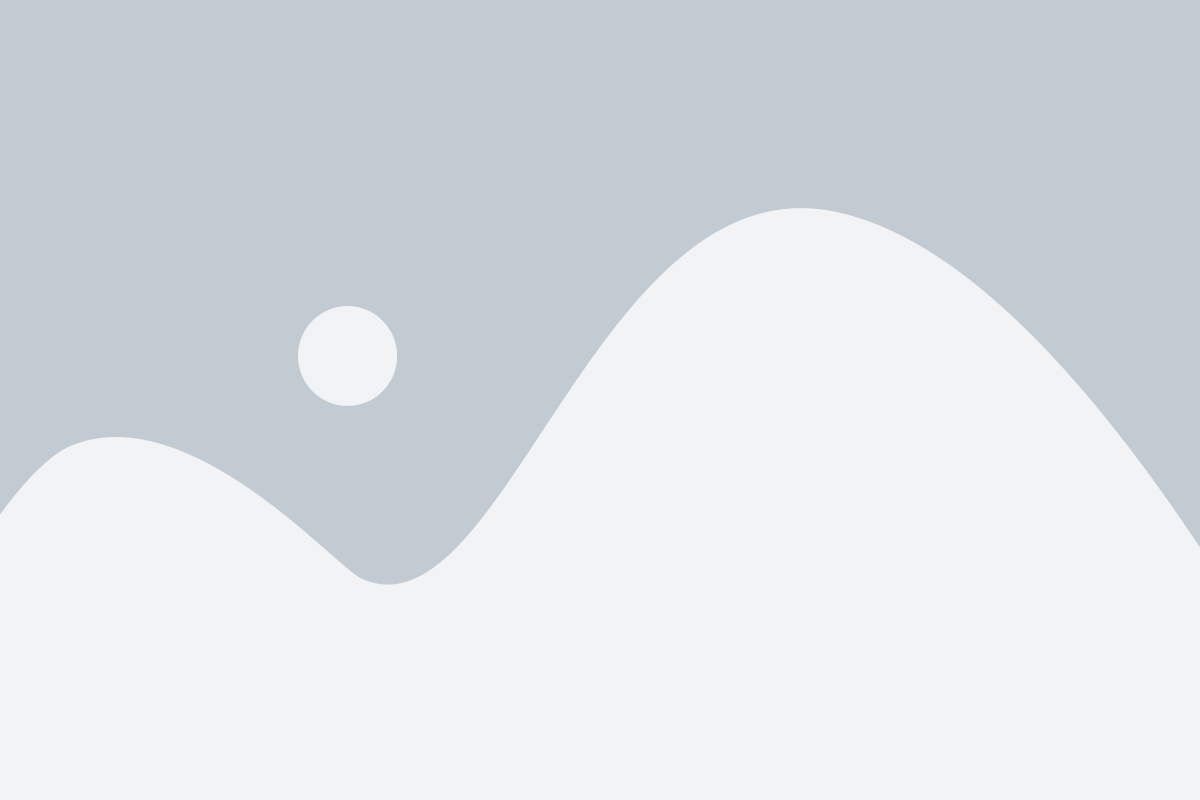
3 Alternative days/ week
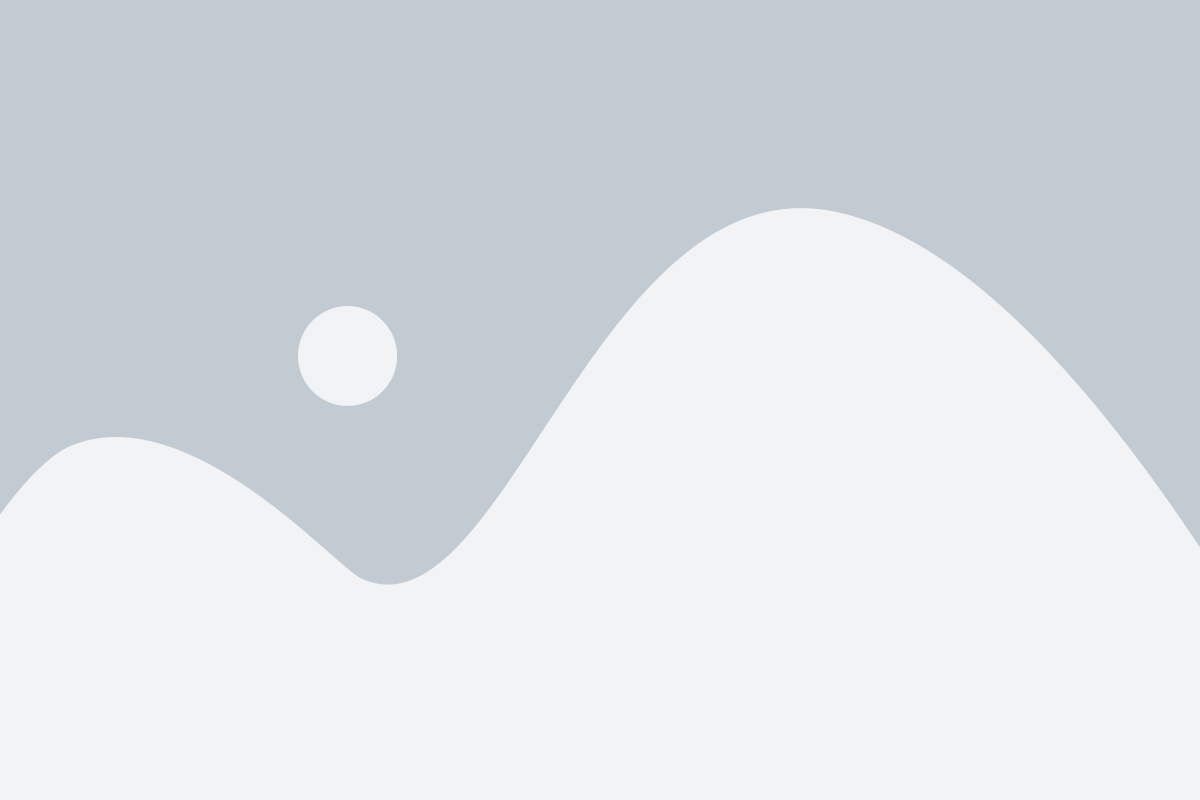
09:30 pm-11:30 pm
Eligibility :-Eligibility: Mechanical Engineering graduates (B.Tech, M.Tech)
Course Overview
The Piping Stress Analysis course is a comprehensive, job-oriented training program designed to meet industry demands. This program combines in-depth theoretical knowledge with practical skills, using industry-standard software such as Caesar II and Navis Works. You will gain the ability to analyze, design, and optimize piping systems, ensuring that they meet safety standards, industry codes, and project-specific requirements. The course covers critical elements such as failure analysis, stress calculation, and dynamic stress analysis, making you fully equipped to handle piping design challenges in industries like oil & gas, refineries, and power plants.
- Module 1: Introduction to Piping Stress Analysis
- Industry Basics: Gain an understanding of the fundamentals of piping stress analysis in oil & gas (O&G) industries, terminologies, and discipline scopes.
- Piping Components: Learn about critical piping elements such as flanges, valves, gaskets, nuts/bolts, fittings, and specialty items.
- Structures in Piping: Understand the basics of structures like pipe racks, platforms, ladders, and technological structures essential to piping systems.
- Software Introduction: Get familiar with Navis Freedom operations for visualizing and managing 3D piping models.
- Module 2: Fundamentals of Piping Stress Analysis
- Introduction to Stress Analysis: Learn why and when piping stress analysis is needed and the different types of stresses in piping systems.
- Failure Theories: Study common failure theories in the context of piping systems.
- Industry Codes and Standards: Understand the critical codes and standards for piping stress analysis, including allowable stress limits.
- Pressure Design: Learn to calculate pressure design for piping components and different types of stress (primary, secondary, and peak stresses).
- Support Selection: Study the types of supports, their selection, and how to calculate span lengths.
- Nozzle Load Calculation: Learn how to generate and calculate allowable nozzle loads for various equipment.
- Flange Leakage Checks: Study the methods for performing flange leakage checks (ASME, NC 3658).
- Stress Critical Line List (SCLL): Develop an understanding of how to prepare and manage a Stress Critical Line List.
- Module 3: Specialty Stress Components
- Expansion Bellows: Learn the selection and application of metallic, rubber, and fabric bellows in piping systems.
- Hose Selection: Study the selection criteria for hoses in piping systems.
- Spring Supports: Understand how to choose variable and constant spring supports.
- Snubbers and Struts: Learn the applications of rigid struts and snubbers in managing stress and dynamic forces.
- Module 4: Pre-Requisites for Stress Analysis
- Design Basis: Understand the essential details derived from the design basis and applicable codes/standards for piping analysis.
- P&ID and Isometric Drawings: Gain practical knowledge of reading and interpreting Piping and Instrumentation Diagrams (P&ID) and isometric drawings for stress analysis.
- Environmental Load Calculations: Learn how to generate seismic coefficients and wind pressure profiles.
- Dynamic Loads: Understand the calculations involved for dynamic loads like slug flow, PSV forces, and water hammer forces.
- Stress Package Preparation: Learn to prepare complete stress packages using P&ID, SCLL, and other supporting documents.
- Interdisciplinary Checks: Collaborate with other disciplines (structural, mechanical, etc.) to ensure consistency across project deliverables.
- Module 5: Stress Routing for Equipment
- Learn stress routing techniques for common equipment, including:
- Pumps
- Heat Exchangers
- Columns and Reactors
- Compressors and Turbines
- Heaters
- Tanks
- Miscellaneous industrial equipment
- Understand the stress analysis requirements and best practices for routing piping connected to these critical pieces of equipment.
- Module 6: Stress Analysis Using Caesar II
- Introduction to Caesar II: Understand the interface and navigation of Caesar II software.
- Configuration and Unit Files: Learn how to prepare Caesar configuration and unit files for different projects.
- Piping Layout Modelling: Master the art of modelling piping layouts in Caesar II based on isometric drawings.
- Material and Support Modelling: Learn how to generate new material data and model various types of supports and restraints.
- Dynamic Load Cases: Understand how to enter seismic data, occasional forces, and settlements in Caesar II.
- Load Case Editor: Explore the options available in the Load Case Editor and learn how to prepare and analyze load cases, including wind data.
- Post-Processing: Learn to interpret displacement, stress, support loads, and nozzle loads. Understand how these results affect other disciplines in the project.
- Dynamic Stress Analysis: Gain an understanding of modal and harmonic analysis in Caesar II for evaluating dynamic stress in piping systems.
- Module 7: Stress Specialty Component Datasheet Preparation
- Datasheet Creation: Learn how to prepare and review datasheets for stress specialty components, including:
- Metallic Bellows
- Rubber Bellows
- Fabric Bellows
- Variable and Constant Springs
- Rigid Struts and Snubbers
- Drawing Approval: Understand the processes involved in approving drawings for these components.