Piping Stress Analysis
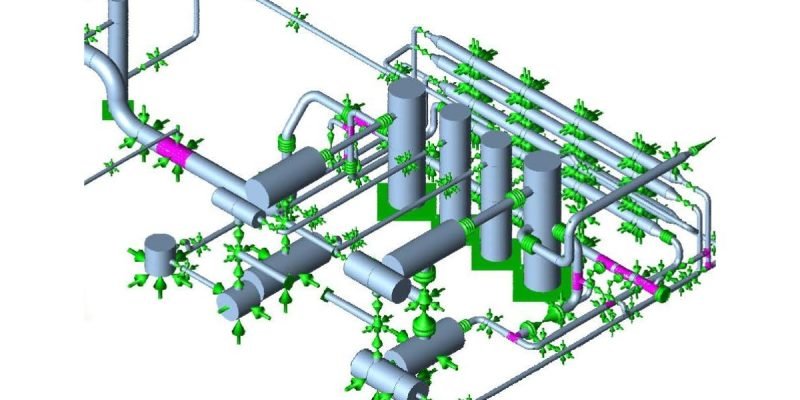
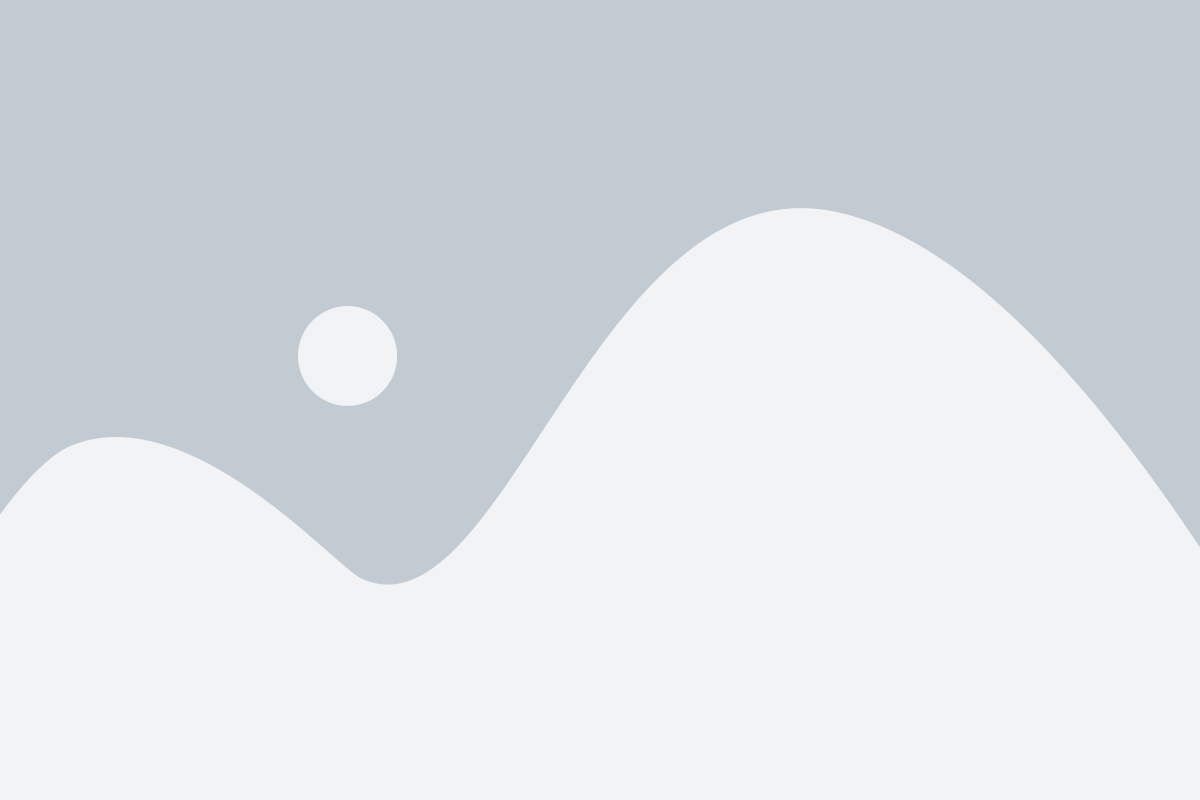
5 Months - 120 Hrs
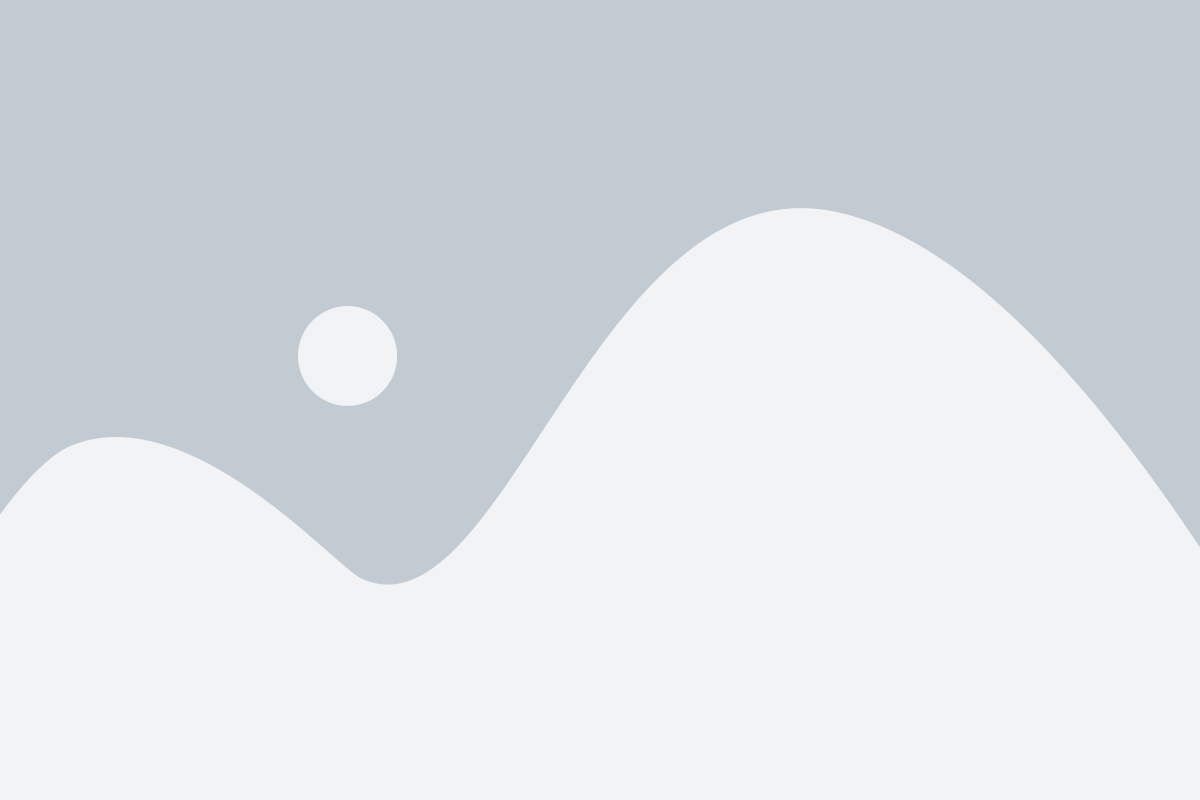
3 Alternative days/ week
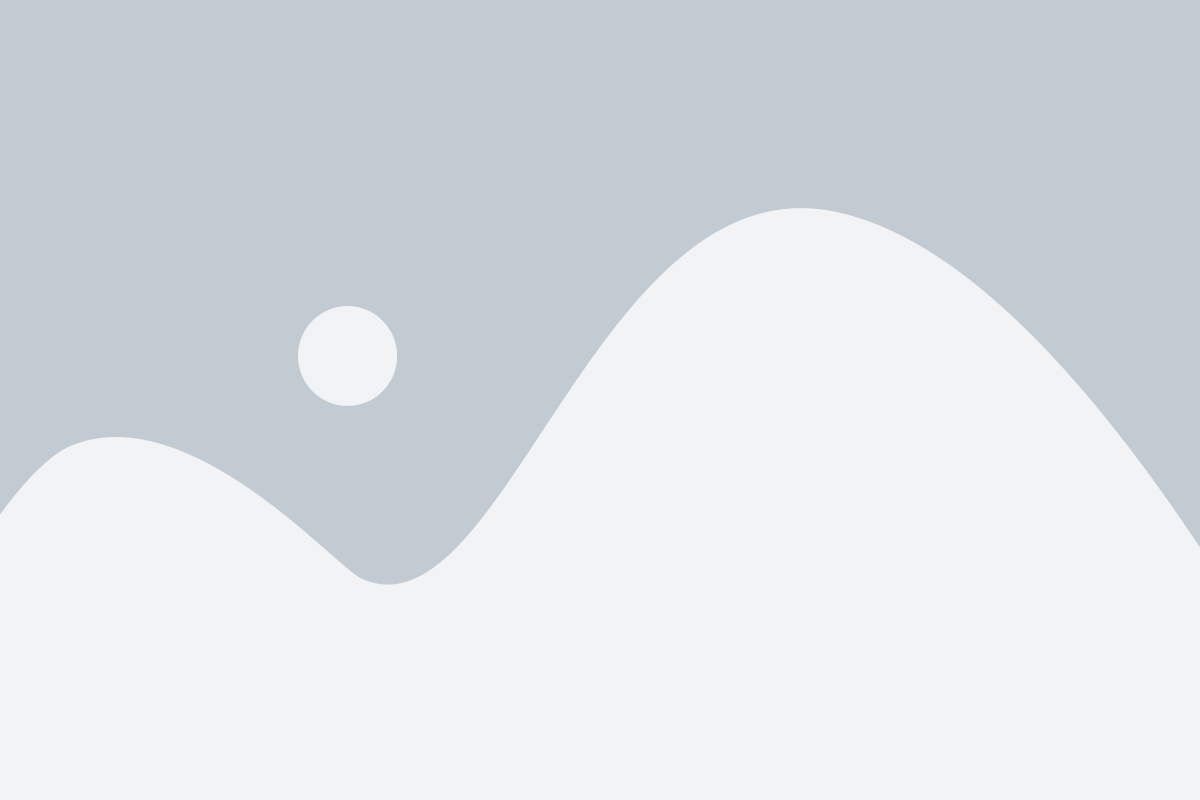
09:30 pm-11:30 pm
Eligibility :- Minimum requirement of a Mechanical Engineering degree
Course Overview
The Piping Stress Analysis course is tailored to meet the demands of industries such as oil and gas, power plants, and refineries. This comprehensive program provides both theoretical knowledge and practical skills, ensuring you are equipped to handle the complex challenges involved in piping stress analysis. Through a combination of project theory and hands-on software training, you will be ready to design and analyze piping systems that comply with industry standards.
- Module 1: Introduction to Piping Stress Analysis
- Understanding the basics of piping stress analysis in the industry.
- Familiarization with oil and gas (O&G) terminologies and the scope of different disciplines.
- Learn about various types of joints, welding techniques, and their applications.
- Study the basics of piping components like flanges, fittings, pipes, valves, gaskets, nuts/bolts, branches, and specialty items.
- Understand the fundamentals of structures such as pipe racks, technological structures, ladders, platforms, and cleats.
- Learn how to navigate and operate Navis Freedom software.
- Module 2: Stress Analysis Fundamentals
- Introduction to the basics of pipe stress analysis, covering the “What, Why, and When” of analysis.
- Study failure theories to understand how and why systems fail.
- Learn about different codes and standards applicable to stresses in piping systems.
- Gain knowledge on the pressure design of components.
- Understand the various types of stresses in piping systems and how to calculate pipe spans.
- Study stress calculations and allowable stress limits.
- Explore the types of supports used in piping systems and how to select appropriate supports.
- Learn about nozzle loads, their generation, and allowable limits for different equipment types.
- Understand how to prepare a Stress Critical Line List (SCLL).
- Study stress specialty components in compliance with industry codes and standards.
- Learn to calculate manhours for projects based on client requirements and design engineering contracts.
- Perform flange leakage checks using methods like pressure equivalent, ASME, and NC 3658.
- Module 3: Stress Specialty Components
- Study the selection and application of expansion bellows (metallic, rubber, fabric).
- Learn about hose selection and its applications in piping systems.
- Study the selection and application of variable and constant spring supports.
- Learn about snubber and rigid strut selection and their applications in piping stress analysis.
- Module 4: Stress Analysis Prerequisites
- Understanding key deliverables in piping stress analysis.
- Learn how to derive details from design bases and relevant codes/standards.
- Gain a basic understanding of P&ID, isometric drawings, the Stress Critical Line List (SCLL), and equipment drawings.
- Learn how to generate seismic coefficients and wind pressure profiles.
- Understand how to calculate forces due to occasional loads such as slug, PSV force, and water hammer force.
- Study how to prepare piping stress packages using P&ID and the Stress Critical Line List.
- Explore interdisciplinary checks and their importance in ensuring project consistency.
- Module 5: Stress Routing for Common Equipment
- Learn stress routing techniques for various types of equipment, including:
- Pumps
- Heat Exchangers
- Columns & Reactors
- Compressors & Turbines
- Heaters
- Tanks
- Miscellaneous equipment used in piping systems.
- Module 6: Stress Analysis Using Caesar II
- Learn how to navigate Caesar II software and understand its interface.
- Prepare Caesar configuration files and unit files.
- Learn to model different equipment types in Caesar II.
- Practice modelling complete piping layouts in Caesar II as per isometric drawings.
- Generate new material details and model supports/restraints.
- Model stress specialty components and input seismic data.
- Enter occasional forces like settlements and nozzle limit checks.
- Understand the Load Case Editor in Caesar II and learn how to create load cases.
- Learn to enter wind data and perform load case analysis.
- Post-process displacements, support loads, and nozzle loads, and understand their significance for other teams.
- Learn how to compare generated stresses with allowable stress limits.
- Introduction to stress analysis for dynamics, including:
- Modal analysis (understanding frequency and its importance).
- Harmonic analysis for mechanical resolution.
- Module 7: Stress Specialty Component Datasheet Preparation
- Learn how to prepare datasheets and drawings for:
- Metallic bellows.
- Rubber and fabric bellows.
- Variable and constant springs.
- Struts and snubbers.
- Understand the approval process for these components.